Shearing Operation Process
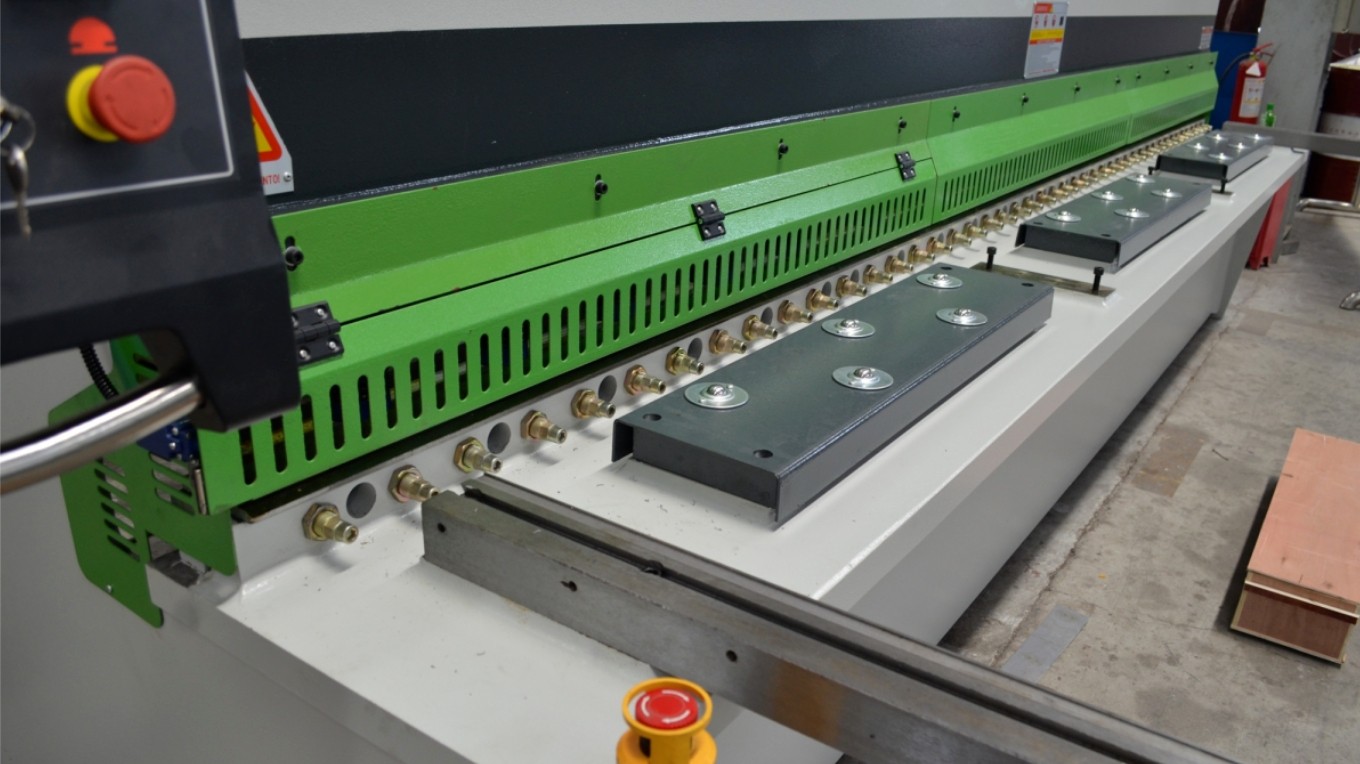
In the shearing process, the shearing machine should be able to ensure the straightness and parallelism requirements of the sheared surface of the sheared plate after shearing and minimize the distortion of the plate to obtain high-quality workpieces. The upper blade of the shearing machine is fixed on the tool holder, and the lower blade is fixed on the workbench. A support ball is installed on the workbench so that the sheet will not be scratched when it slides on it.
The stopper is used for the positioning of the sheet, and the position is adjusted by the motor. The pressing cylinder is used to press the sheet to prevent the sheet from moving during shearing. Guardrails are safety devices to prevent accidents at work. The return journey generally relies on nitrogen, which is fast and has a small impact. So what are the operating procedures for shearing plate processing? Let's introduce it to you below!
Shearing Operation Process
1. Preparation: Check whether the equipment is in normal condition and perform necessary maintenance and cleaning. Confirm that the size and specifications of the die cutter meet the requirements.
2. Adjust the cutting length: Set the cutting length according to your needs, and adjust the gap of the knife die according to the material thickness.
3. Install the material: place the metal sheet to be processed on the work table of the shearing machine, and fix the workpiece to prevent it from moving during the cutting process.
4. Start cutting: Start the shearing machine, operate it according to the instructions in the equipment operation manual, make the die lower, and cut the material.
5. Check the results: After the cutting is completed, check whether the surface of the workpiece is flat and smooth and whether the cutting is accurate.
6. Clean-up work: collect and dispose of waste materials, and clean and store equipment properly.
Precautions for Shearing Operation
1. It is not allowed to cut laminated sheets, trim the edges of raw-edged sheets, and cut narrow sheets and short sheets that cannot be pressed tightly.
2. The gap between the knife plates should be adjusted according to the thickness of the plate, but it should not be greater than 1/30 of the maximum thickness of the plate. The knife plate should be fastened firmly, and the upper and lower knife plate surfaces should be kept parallel. After adjustment, manual turning inspection should be used to avoid accidents.
3. The cutting edge of the blade should be kept sharp. If the cutting edge becomes blunt or cracked, it should be replaced in time.
4. When cutting, the pressing device should firmly press the sheet, and it is not allowed to cut under the state of not being pressed tightly.
5. For equipment with hydraulic devices, other than throttling valves, other hydraulic valves are not allowed to be adjusted privately.
6. For the thickness of the sheared sheet by the hydraulic pendulum shearing machine, should be determined according to the "Curve of the Relationship between the Ultimate Strength of the Sheet and the Thickness of the Sheet".
The above is the introduction to the shearing process and precautions. If you want to know more or want to buy a shearing machine, please contact us.
HENGLI is a professional custom shearing machine manufacturer. Our company has more than 10 innovation patents and nearly 30 utility creation patents. As one of the national industry standard-setting members, we have core technologies and core products with independent intellectual property rights. The main products are synchronized with the world's advanced technology and are widely used in the pillar industries of the national economy such as automobile manufacturing and parts processing, iron and steel metallurgical processing, electric power, and metal packaging.