Unlocking the Value: Sheet Metal Shearing Costs and Benefits
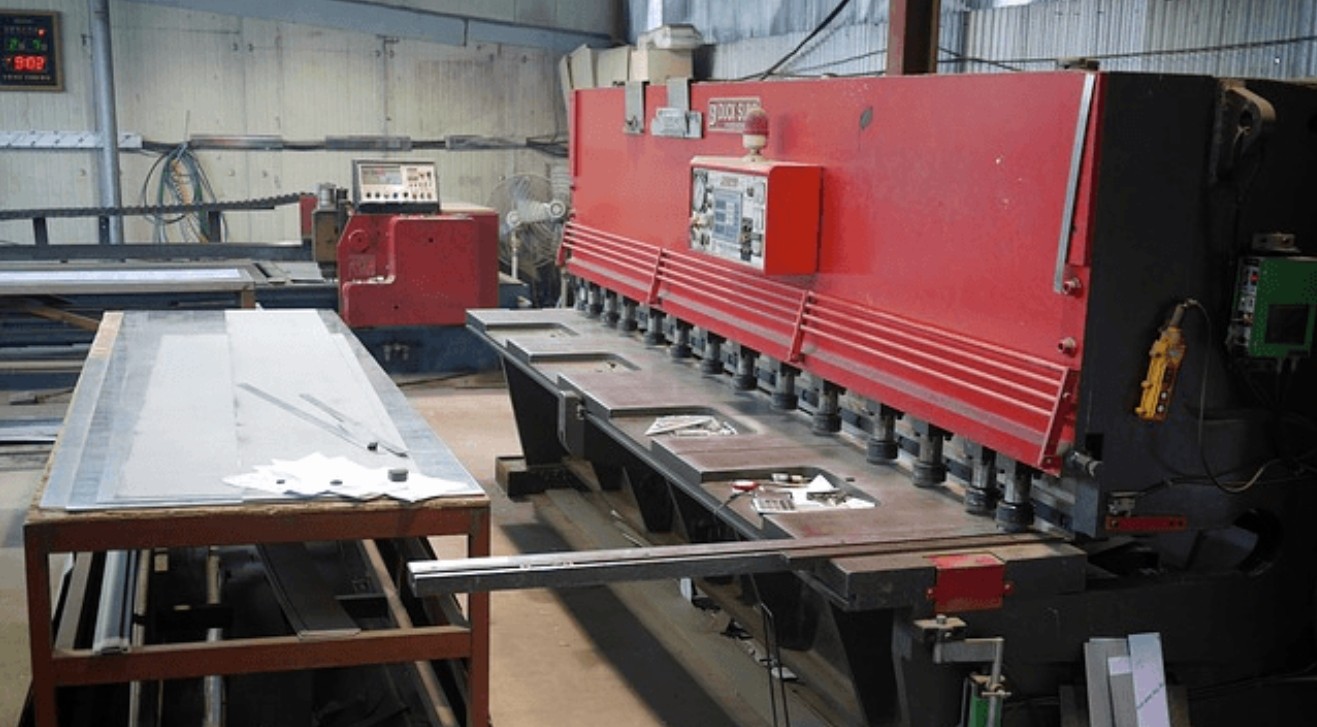
When it comes to sheet metal fabrication, one of the essential processes is sheet metal shearing. This process involves cutting large sheets of metal into smaller, more manageable sizes. However, investing in a sheet metal shearing device can be a significant expense for businesses. In this article, we will explore the factors that affect the cost of a sheet metal shearing device and provide insights into cost-effective shearing practices.
What is Sheet Metal Shearing?
Sheet metal shearing is a metal fabrication process that involves cutting large sheets of metal into smaller pieces. It is commonly used in industries such as manufacturing, construction, and automotive. The shearing process typically utilizes a specialized machine, known as a shearing device, to make straight-line cuts through the metal sheets.
Importance of Sheet Metal Shearing
Sheet metal shearing plays a vital role in various industries. It allows manufacturers to create precise cuts, ensuring the accurate sizing of metal parts and components. This process is crucial for achieving the desired dimensions and shapes required for different applications. Whether it's producing custom parts or mass production, sheet metal shearing is indispensable in the fabrication process.
Factors Affecting the Cost of Sheet Metal Shearing Device
Several factors contribute to the overall cost of a sheet metal shearing device. Understanding these factors will help businesses make informed decisions when investing in such equipment. Here are the key factors to consider:
Machine Size and Capacity: The size and cutting capacity of the shearing device greatly impact its cost. Machines with larger cutting lengths and higher thickness capacities tend to be more expensive.
Cutting Mechanism: Sheet metal shearing devices can employ different cutting mechanisms, such as the guillotine, swing beam, or hydraulic. The complexity and precision of the cutting mechanism can influence the device's cost.
Material Type and Thickness: Different sheet metals require varying cutting forces and specialized blades. Shearing devices designed to handle thicker or harder metals may come at a higher price due to their robust construction.
Automation Features: Automated shearing devices equipped with features like CNC controls, back gauges, and automatic feeding systems offer increased efficiency and precision. However, these advanced features may contribute to a higher cost.
Brand and Quality: Reputable brands with a history of producing high-quality shearing devices often come with a premium price. Investing in a trusted brand ensures reliability, longevity, and excellent customer support.
Additional Accessories: Some shearing devices may require additional accessories or optional attachments for specific applications. These accessories can add to the overall cost of the equipment.
Benefits of Investing in a Quality Shearing Device
While the initial cost of a sheet metal shearing device might seem significant, investing in a quality machine offers several long-term benefits. These include:
Improved Efficiency: A reliable shearing device enhances productivity by providing accurate and consistent cuts, reducing material waste, and minimizing downtime.
Enhanced Precision: Quality shearing devices deliver precise cuts, ensuring the desired dimensions and minimizing errors. This level of accuracy is crucial for maintaining the integrity of the fabricated parts.
Time and Cost Savings: Efficient shearing devices can streamline production processes, reducing labor costs and minimizing material waste. The ability to complete cuts accurately and swiftly contributes to overall cost savings.
Versatility and Flexibility: Investing in a versatile shearing device allows businesses to work with a wide range of sheet metal types and thicknesses, accommodating various projects and expanding their capabilities.
Longevity and Durability: High-quality shearing devices are built to withstand rigorous usage over an extended period. They are made from robust materials and undergo stringent quality control measures, ensuring long-lasting performance and reliability.
Tips for Cost-Effective Sheet Metal Shearing
While the cost of a sheet metal shearing device is an important consideration, it is equally essential to adopt cost-effective practices to maximize its value. Here are some tips to optimize sheet metal shearing operations:
Regular Maintenance: Ensure routine maintenance of the shearing device to keep it in optimal condition. This includes lubricating moving parts, inspecting blades for sharpness, and addressing any potential issues promptly.
Proper Blade Selection: Choose the appropriate blade type and material for different sheet metal applications. Using the right blade ensures clean cuts, prolongs blade life, and minimizes the need for frequent replacements.
Optimize Material Usage: Plan sheet layouts effectively to minimize material waste. By optimizing the use of each sheet, businesses can maximize their yield and reduce costs associated with excessive scrap.
Employee Training: Provide comprehensive training to operators to ensure they are proficient in operating the shearing device. Proper technique and handling can prevent errors, reduce accidents, and increase overall efficiency.
Automation Integration: Consider integrating automation features, such as CNC controls and automatic feeding systems, to enhance productivity and reduce human error. Automation streamlines processes and improves overall workflow efficiency.
Investing in a quality sheet metal shearing device is a significant decision for businesses involved in metal fabrication. Understanding the factors influencing the cost and the benefits of such equipment is crucial for making informed choices. By considering machine size, cutting mechanism, material type, automation features, brand, and additional accessories, businesses can select the right shearing device for their specific needs. Implementing cost-effective practices and prioritizing regular maintenance will ensure optimal performance, enhanced efficiency, and long-term cost savings.
The above has introduced some factors that affect the cost of sheet metal shearing devices, if you want to purchase sheet metal shearing devices for your business, please contact us.
Hengli is a professional custom sheet metal cutting equipment manufacturer in China. The main products are synchronized with the world's advanced technology and are widely used in the pillar industries of the national economy such as automobile manufacturing and parts processing, iron and steel metallurgical processing, electric power, and metal packaging. The company aims to be a technology pioneer and market leader in the metal blanket forming industry, insists on innovation, builds a brand, and prospers China's equipment manufacturing.