How to Reduce Material Waste in Silicon Steel Slitting Lines?
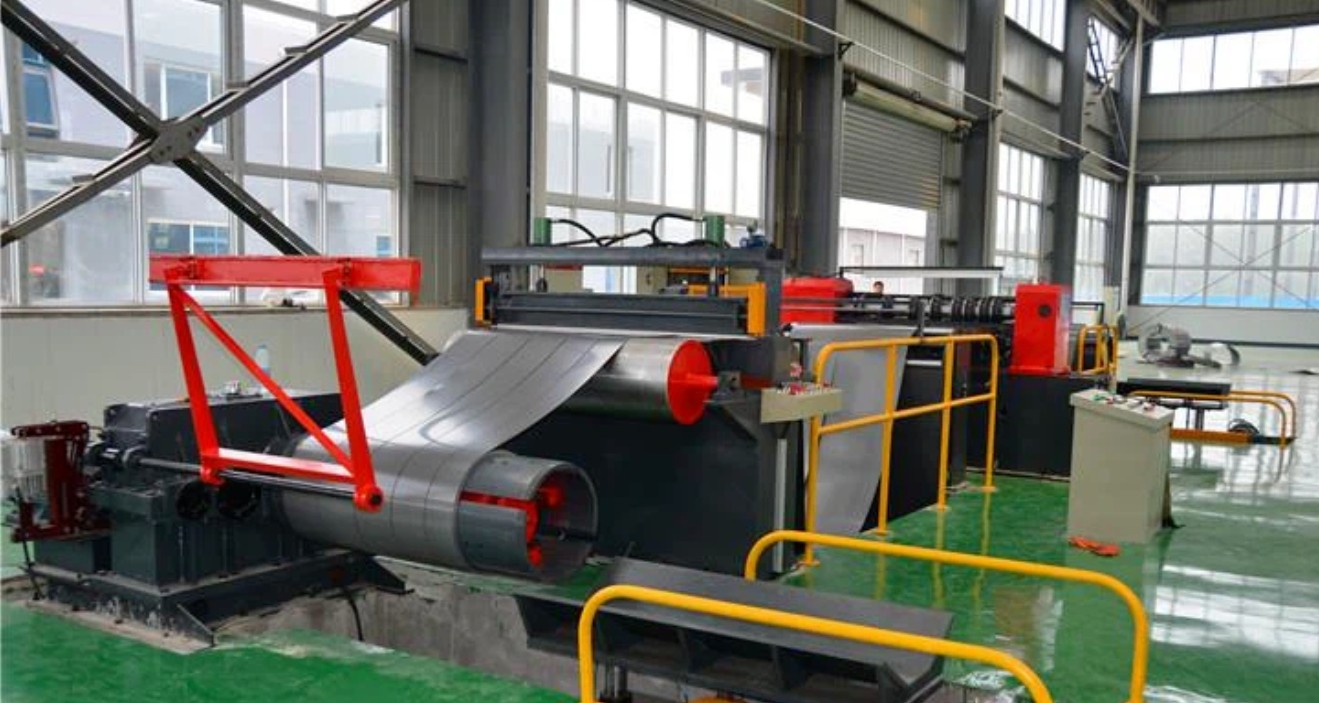
Silicon steel, also known as electrical steel, is an important material in the production of power transformers, motors, and generators. To manufacture precision parts, silicon steel slitting lines are used, but they often create a lot of material waste. This article will delve into the world of silicon steel slitting lines, explore the consequences of material waste, and discuss effective strategies for reducing waste in this critical manufacturing process.
Understand the Silicon Steel Slitting Line
A silicon steel slitting line is an industrial machine designed to process large rolls of silicon steel into narrower strips. These strips are used in the manufacture of laminations for transformers, motors, and generators. The slitting process involves uncoiling, straightening, and cutting the steel to precise dimensions, all of which can create waste if not handled properly.
Impact of Material Waste
Material waste during silicon steel manufacturing can have serious consequences, impacting the industry's economy and environment.
Economic Impact:
Increased production costs: When a large amount of silicon steel is wasted during the slitting process, it directly translates into higher production costs. Material waste means financial losses for manufacturers because the raw materials they invested in are not fully utilized. This in turn leads to an increase in product prices, making their products less competitive in the market.
Waste of resources: Material waste means wasting precious resources because silicon steel is a key component of the motor. Utilization of these resources is not only economical but also critical to meeting the growing demands of the electrical industry.
Impact on the Environment:
Resource depletion: The production of silicon steel consumes various resources, including iron ore, coal and energy. When a large proportion of materials end up as waste, it accelerates the depletion of these limited and non-renewable resources.
Pollution and carbon footprint: Waste materials must be disposed of or recycled. This disposal process pollutes and creates a carbon footprint because it often involves transportation, energy consumption, and emissions from waste management facilities. The environmental impacts of this process are harmful, and reducing waste can significantly mitigate these impacts.
Sustainable Manufacturing: In an era of increasing focus on sustainability, material waste in manufacturing is increasingly frowned upon. Companies that reduce waste not only minimize their impact on the environment but also follow sustainable business practices, which are attractive to eco-conscious consumers.
Technology to Reduce Material Waste
Reducing material waste in silicon steel slitting lines is crucial to making the manufacturing process more efficient and sustainable. Here are some techniques that can effectively reduce waste:
1. Achieve Precision Cutting
One of the major sources of waste on slitting lines is imprecise cutting. To reduce material waste, manufacturers can invest in cutting machines with superior precision. Precision cutting minimizes the amount of remaining material, ensuring more efficient use of resources.
2. Strengthen the lubrication System
Effective lubrication is essential to reduce friction during slitting. Well-lubricated machines generate less heat and wear and tear on cutting tools, resulting in less waste. Regular maintenance of your lubrication system is essential to ensure smooth operation.
3. Quality Control Measures
Implementing strong quality control measures can help detect defects early in the process, preventing the production of defective components that end up as waste. This may involve automated inspection systems and online testing to catch errors before they result in wasted material.
4. The Role of Automation
Automation plays a key role in minimizing material waste. Automated systems adjust machine settings in real-time, ensuring optimal cuts and reducing waste. Advanced software can also predict potential problems and prevent costly mistakes from happening.
5. Improve Maintenance Practices
Regular maintenance of the slitting line is essential to reduce waste. Well-maintained machines are more efficient, produce less waste, and last longer. Routine inspection, cleaning, and timely replacement of worn parts are key practices in reducing waste.
6. Sustainable Material Handling
Handling the material efficiently is just as important as the cutting process itself. Implementing sustainable material handling practices can reduce damage and waste during transportation and storage. This includes using appropriate packaging, minimizing material handling, and ensuring appropriate storage conditions.
In Conclusion
Reducing material waste in silicon steel slitting lines is a key step towards more sustainable and cost-effective manufacturing. By implementing precision cutting, enhancing lubrication systems, employing quality control measures, and adopting automation and sustainable practices, manufacturers can have a significant impact on their bottom line and the environment. The above briefly introduces the method of reducing material waste in silicon steel slitting lines. If you want to know more or you want to purchase silicon steel slitting lines, please contact us.
Hengli is a professional custom silicon steel shearing equipment manufacturer. It is a national high-tech enterprise specializing in the R&D and manufacturing of high-end industrial automation equipment. It is one of the major suppliers of sheet metal cutting and forming automation equipment in China. The main products are in sync with the world's advanced technologies and are widely used in pillar industries of the national economy such as automobile manufacturing and parts processing, steel metallurgical processing, electric power, and metal packaging.