Maximizing Output: Strategies for Increasing Output with Cut-to-Length Lines
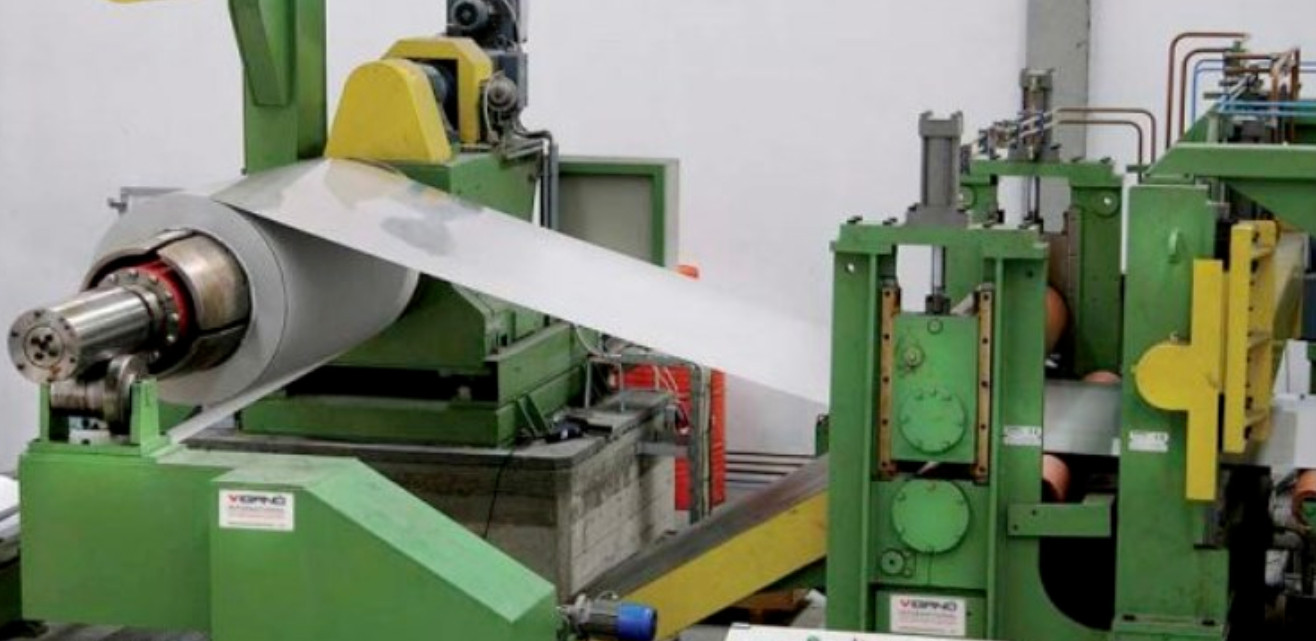
In today's fast-paced manufacturing environment, optimizing production processes is the focus for companies to remain competitive. One technology that has proven to be a game-changer in this regard is cutting lines (CTLs). This article explores strategies for maximizing output through the effective use of CTL in a variety of production environments.
What Is Fixed Length Cutting Line?
Cut-to-length lines, often abbreviated as CTL, represent a complex and integral aspect of modern manufacturing processes in different industries. At its core, cut-to-length cutting lines are a precision-driven technology designed to cut metal coils into specific and precise lengths, becoming key to manufacturing a variety of end products. The cut-to-length cutting line system consists of key components such as decoilers, levelers, and cutters, operating in a synchronized manner to provide unrivaled precision and efficiency. The process solves the inherent challenges of flatness variation in metal coils, enabling the production of uniformly cut materials critical in industries such as automotive, construction, and appliances.
In the manufacturing sector, cut-to-length cutting lines play a key role in optimizing production results. Its importance lies in its ability to provide unparalleled cutting precision, increase efficiency, and minimize waste. As the industry evolves, cut-to-length cutting lines stand out as a versatile solution for a variety of materials, making them a cornerstone technology for companies aiming to improve the accuracy, speed, and cost-effectiveness of their production processes.
Maximize Output
Yield maximization is a fundamental concept in the field of production and manufacturing, encompassing the strategic pursuit of achieving the highest possible levels of productivity and efficiency. At its core, output maximization involves optimizing the use of resources, whether labor, materials, or machinery, to produce the maximum amount of a good or service in a given time frame. This overall goal goes beyond pure volume to encompass broader operational efficiency, cost efficiency, and overall performance in meeting market needs. Essentially, it is about achieving the pinnacle of productivity without compromising on quality or sustainability, a dynamic balancing act that defines success in the contemporary industrial landscape.
Strategies to Increase Output Through Cut-to-Length Lines
Invest in Advanced CTL Technology: Embracing the latest advances in CTL technology is fundamental. Upgrading to a cutting-edge system ensures increased accuracy, speed, and adaptability, directly impacting overall output. Advanced CTL technology often has features that optimize the cutting process, minimize errors, and maximize efficiency.
Implement Predictive Maintenance: A proactive maintenance strategy is critical for uninterrupted cut-to-length cutting line operation. Predictive maintenance based on data analytics and machine learning can identify potential problems before they escalate. By implementing predictive maintenance methods, manufacturers can reduce downtime and ensure that cut-to-length cutting line systems are always operating at peak performance levels.
Train Personnel for Optimal CTL Operation: The efficiency of a cut-to-length line system is closely related to the proficiency of the operator. A comprehensive training program ensures employees are proficient in the nuances of cut-to-length line operation. From understanding technical complexities to solving common problems, a skilled workforce is critical to maximizing the benefits of cut-to-length cutting-line technology.
Optimize Material Handling: Seamless material handling is a key aspect of production efficiency. Integrating cut-to-length cutting lines with smart material handling systems ensures a continuous flow of materials, reduces idle time, and increases overall efficiency. The synergy between the cut-to-length cutting line and the material handling system simplifies the entire production process.
Quality Control Measures: Precision and quality go hand in hand. Integrating strong quality control measures into the cut-to-length process ensures that every cut is made to the required standard. Not only does this eliminate the need for rework, but it also helps make the production line smoother and more efficient.
Production Automation: While automation is a powerful ally in maximizing output, it requires strategic implementation. Automation of routine tasks in the cut-to-length process reduces manual intervention, increases speed, and minimizes errors. However, a balanced approach is crucial to keeping production flexible and adaptable.
Customization and Flexibility: Tailoring your cut-to-length line process to suit different materials and product specifications is a strategic move. The ability to customize cut-to-length line operations ensures adaptability to different market needs, providing a competitive advantage in a dynamic manufacturing environment.
Optimize Material Handling
In modern manufacturing where efficiency and precision are critical, optimizing material handling is a key strategy. This approach involves careful management and simplification of the movement, storage, and control of materials throughout the production process. The core objective is to ensure a seamless and continuous flow of materials, minimize delays, reduce idle time, and ultimately improve the overall efficiency of manufacturing operations. In an era where just-in-time and lean manufacturing principles dominate, the optimization of material handling has become not only a logistics necessity but also a strategic imperative for companies striving to remain competitive in a dynamic market.
The importance of optimizing material handling spans across industries, from automotive and aerospace to electronics and more. Efficient material handling not only helps save costs, but also plays a vital role in minimizing errors, improving workplace safety, and ensuring production processes reach their full potential. By integrating advanced technology and intelligent systems into material handling practices, manufacturers can achieve a delicate balance between speed and precision, creating a production environment that is not only efficient but also adaptable to changing market demands. As we delve deeper into the nuances of optimizing material handling, it’s clear that this strategic approach is at the forefront of reshaping the way the industry manages resources and drives itself toward operational excellence.
In Conclusion
In summary, maximizing manufacturing output is a multi-faceted endeavor that involves a strategic approach utilizing technologies such as cut-to-length cutting lines. By investing in advanced technology, optimizing material handling, implementing quality control measures, and keeping up with future trends, companies can improve production efficiency and ensure long-term success in a highly competitive market.
The above briefly introduces the benefits and necessity of increasing output through fixed-length cutting production lines. If you want to know more about fixed-length cutting production lines or you want to order fixed-length cutting production lines, please contact us.
Hengli is a professional custom-length cutting production line manufacturer. It is a national high-tech enterprise specializing in the R&D and manufacturing of high-end industrial automation equipment. It is one of the major suppliers of sheet metal cutting and forming automation equipment in China. The main products are in sync with the world's advanced technologies and are widely used in pillar industries of the national economy such as automobile manufacturing and parts processing, steel metallurgical processing, electric power, and metal packaging.
1. Leveler for high strength steel or aluminum
2. High precision digital level,
1.Suitable material:CRC,GI,EG, stainless coil
2.Material thickness:0.2 -3.0mm
3.Material width:400-1800mm