Principle and Maintenance of Cut-to-Length Production Line
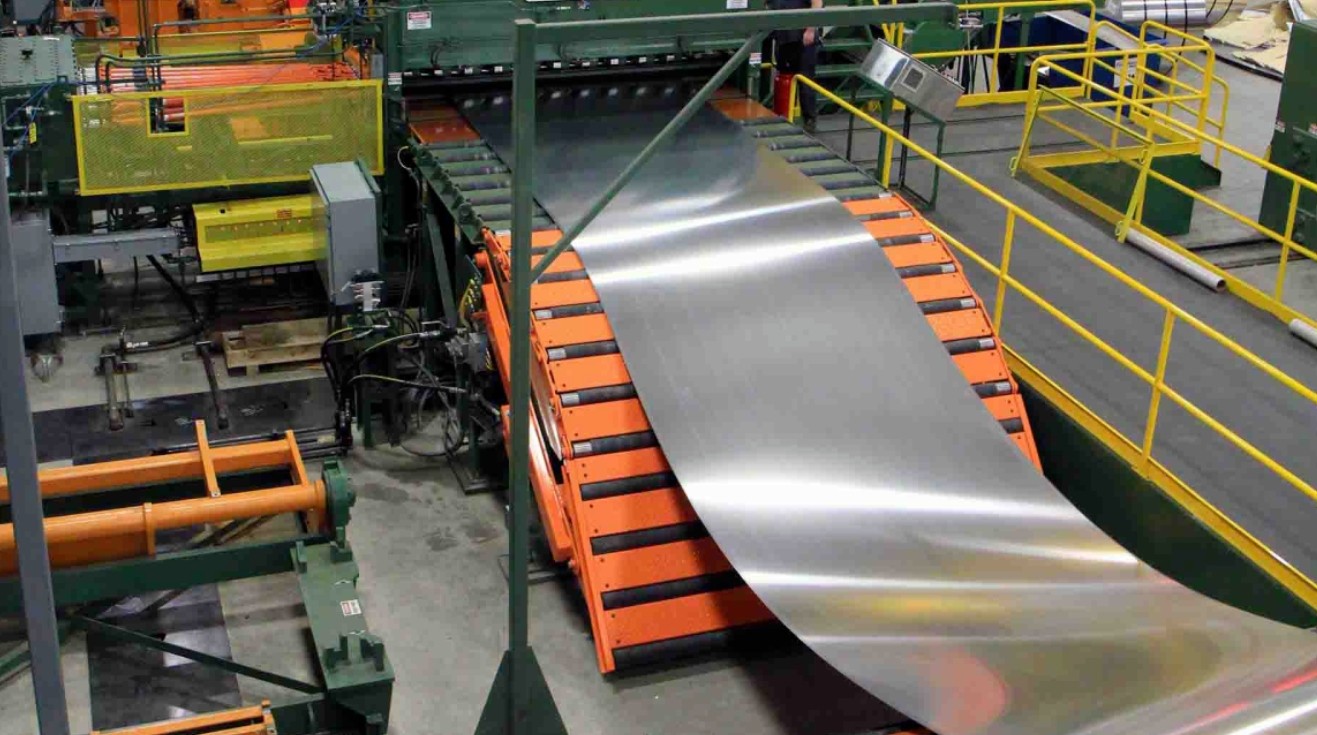
In the rapidly evolving industrial operating landscape, the importance of efficiency and precision cannot be overstated. Cut-to-length lines (CTL) have become an indispensable tool and play a key role in achieving these goals across different industries. In this exploration, we'll reveal the guidelines for managing a CTL machine, examine its essential components, and delve into recommended maintenance practices.
Definition of Cut-to-Length Cutting Line
Cut-to-length (CTL) cutting lines are advanced industrial machines designed to automate and streamline the process of converting coiled sheet metal into precise, custom lengths. This innovative system plays a vital role in improving the efficiency and accuracy of metal processing in various industries. The main goal of a CTL cutting line is to efficiently uncoil metal coils, straighten the sheet to remove any imperfections, and cut it precisely to the required length. By automating these tasks, CTL cutting lines minimize material waste, reduce production time, and contribute to the overall optimization of the manufacturing process.
The core of the CTL cutting line consists of multiple interconnected components that work seamlessly to achieve the desired results. The machine usually includes a decompiler to uncoil the metal coil, a straightening device to correct any deformation of the sheet and a cutting device equipped with precision blades for precise length customization. The conveyor system helps the cut sheets move smoothly through the production line, and the control panel serves as a command center, allowing operators to enter parameters, monitor the process, and make real-time adjustments. The combination of mechanical precision and automation makes CTL cutting lines indispensable in industries where precision, efficiency, and customization are critical.
Principle of Fixed Length Cutting Line
The principle of the cut-to-length line involves a systematic, automated approach to the efficient and precise processing of sheet metal. These machines are designed to perform a basic series of steps to transform coiled metal into specific, predetermined lengths. The basic principles can be divided into several key stages:
Uncoiling: The process begins with the uncoiling stage, where the metal coil is uncoiled to provide a continuous feed of material. This step lays the foundation for subsequent operations.
Straightening: Sheet metal often has imperfections from the coiling process. Straightening is a key principle in correcting these deformities, ensuring a smooth surface and even a precise cut.
Cutting: A cutting unit equipped with advanced blades performs the final step by cutting the metal sheet into specified lengths. This stage requires precise maintenance of tight tolerances and ensuring the expected results.
Automation and Precision: CTL lines combine sophisticated automation and precision mechanisms. This includes the integration of sensor technology that monitors various parameters throughout the process, as well as advanced control systems. Together, these elements contribute to the accuracy and efficiency of CTL machines.
By adhering to these principles, cut-to-length lines enable industries to achieve optimal results in terms of material utilization, production speed, and delivery of precisely cut metal sheets customized to specific requirements.
Maintenance Practice of Cut-to-Length Cutting Lines
Maintenance practices for cut-to-length (CTL) cutting lines are critical to ensuring the continued efficiency and reliability of these complex industrial machines. Regular and proactive maintenance helps prevent breakdowns, reduce downtime, and extend the life of your equipment. The following are key maintenance practices related to CTL cutting lines:
Regular Inspections: Frequent and thorough inspections of all components are crucial. This includes inspection of the decompiler, straightening unit, cutting blades, conveyor system, and control panel. Early detection of potential problems allows timely intervention and prevention of more widespread damage.
Lubrication: Proper lubrication of moving parts is critical to smooth operation. Regularly applying lubricant to bearings, rollers, and other mechanical parts minimizes friction, reduces wear, and ensures optimal performance.
Software Updates: Keeping control systems and software up to date is critical. Regular updates to the software that manages CTL machines can incorporate improvements, bug fixes, and additional features that help enhance functionality.
Emergency Repairs: It is critical to establish protocols for responding quickly to unexpected breakdowns. Having a designated emergency repair team ensures issues are resolved promptly, minimizing downtime and preventing interruptions to the production process.
These maintenance practices not only focus on solving existing problems but also on prevention. Regular maintenance helps identify and correct potential problems before they escalate, thereby reducing the risk of major failures and optimizing the overall performance of your cut-to-length line. Implementing a comprehensive maintenance strategy is key to maximizing the efficiency and longevity of these critical industrial machines.
In Conclusion
In short, the cut-to-length production line is a beacon of innovation in modern manufacturing. Its principles, combined with regular maintenance practices, ensure a seamless and efficient production process. Applications range from automotive to metal manufacturing, contributing to the success of various industries.
The above briefly introduces the maintenance and working principle of cut-to-length lines. If you want to know more about cut-to-length lines, or if you want to purchase cut-to-length lines, please contact us.
HENGLI is a professional cut-to-length cutting line manufacturer. Our company has more than 10 innovation patents and nearly 30 utility creation patents. As one of the national industry standard members, we have core technologies and core products with independent intellectual property rights. The main products are synchronized with the world's advanced technology and are widely used in pillar industries of the national economy, such as automobile manufacturing and parts processing, iron and steel metallurgical processing, electric power and metal packaging.