Common Problems and Solutions for Sheet Metal Rotary Shears
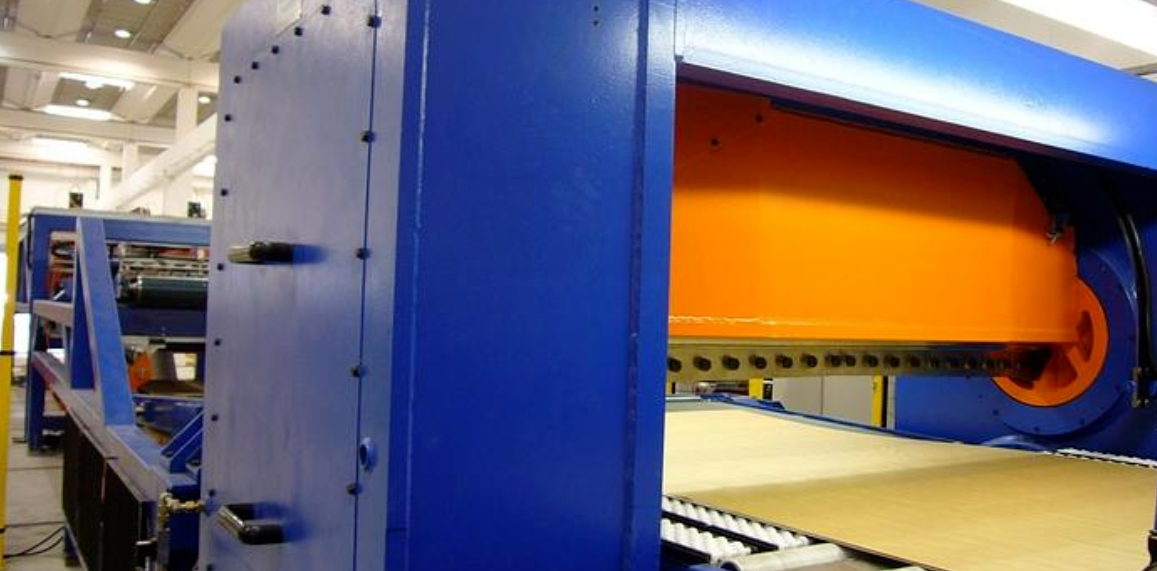
In sheet metal processing, rotary shears play a vital role in achieving precise cuts and maintaining operational efficiency. However, like any machinery, sheet metal rotary shears can experience a variety of problems that can affect their performance. At Hengli, we understand the importance of keeping your equipment in top condition. In this article, we will explore some of the most common problems facing rotary shears and provide effective solutions to ensure your operation runs smoothly.
1. Dull Cutting Blades
One of the most common problems with rotary shears is wear and tear on the cutting blades. Dull blades can lead to poor cut quality, increased material waste, and excessive machine strain.
Solution: Regularly inspect and sharpen or replace cutting blades as needed. It is recommended to develop a maintenance schedule that includes inspecting the blades after a specific number of cuts or operating hours. Using Hengli's quality blades can also improve cutting efficiency and durability.
2. Blade Misalignment
Misalignment of the top and bottom blades can lead to uneven cutting, increased friction, and possible damage to the machine. This problem is usually caused by improper installation or long-term wear.
Solution: Use the appropriate tools to regularly check the alignment of the blades. If misalignment is detected, adjust the position of the blade according to the manufacturer's guidance. Ensuring that the blade is properly installed from the beginning can prevent this problem.
3. Inconsistent Cutting Speeds
Inconsistent cutting speeds can cause variations in cut quality and increase production time. This inconsistency can be caused by motor problems, insufficient power supply, or mechanical failure.
Solution: Check the motor and power supply for any anomalies. Make sure the machine is receiving the correct voltage and that all electrical connections are secure. In addition, performing routine maintenance on the motor can help prevent speed inconsistencies.
4. Excessive Vibrations
Excessive vibrations during operation can indicate an underlying mechanical problem, such as loose parts or worn bearings. This vibration can cause further mechanical damage and reduced cutting accuracy.
Solution: Perform a thorough inspection of the rotary shear to determine if there are any loose parts or worn components. Tighten any loose screws and replace any damaged bearings. Implementing a routine maintenance schedule can help detect these problems early, thereby reducing the risk of excessive vibration.
5. Material Jams
Material jams are when sheet metal gets stuck in the shear, causing the cutting process to be interrupted. This can be caused by incorrect material thickness or improper feeding technique.
Solution: Make sure the material fed into the rotary shear is within the thickness range specified for the machine. Train operators on proper feeding techniques to minimize the risk of material jams. Also, consider investing in a Hengli rotary shear model that is designed to handle a wider range of material types and thicknesses.
6. Overheating
Overheating can be a serious problem that can lead to equipment failure and unsafe operating conditions. This problem can be caused by prolonged use, insufficient lubrication, or a clogged cooling system.
Solution: Monitor the machine's operating temperature during use. Make sure the lubrication system is functioning properly and all moving parts are adequately lubricated. Clean all cooling vents or systems regularly to promote proper airflow and heat dissipation.
7. Electrical Failure
Electrical problems can cause the rotary shear to malfunction or stop operating altogether. These failures can be caused by faulty wiring, blown fuses, or a faulty control panel.
Solution: Regularly inspect electrical components, including wiring and fuses. Replace any damaged parts immediately to prevent further problems. Keeping a stock of spare parts can also minimize downtime in the event of an electrical failure.
8. Improper Maintenance
Neglecting regular maintenance can lead to a host of problems, including decreased efficiency and increased wear on components. Lack of maintenance can significantly shorten the life of your rotary shear.
Solution: Develop a comprehensive maintenance plan that includes daily, weekly, and monthly inspections. The plan should cover all critical aspects of the machine, including lubrication, blade condition, and electrical systems. Training operators on proper maintenance practices are also critical to ensure longevity and efficiency.
Conclusion
Maintaining the performance of your metal plate rotary shear is critical to any metalworking operation. By addressing common issues such as blunt blades, misalignment, and overheating, you can ensure your shears are operating at peak efficiency. At Hengli, we are committed to providing high-quality products and solutions to enhance your shearing process. Implementing regular maintenance practices and promptly addressing issues that arise will not only improve your machine's performance but also extend its life.
We are a leading metal plate rotary shears manufacturer. Hengli is guided by innovation and cutting-edge technology. Our main product line is seamlessly connected to the world's advanced technology and is widely used in key areas of the national economy such as automotive manufacturing and parts processing, steel metallurgical processing, power, and metal packaging.
If you encounter persistent problems or need help, feel free to contact us for expert advice and support. Together, we will optimize your metal shearing operation and achieve outstanding results.