Safety First: Best Practices for Operating a Gang Slitter
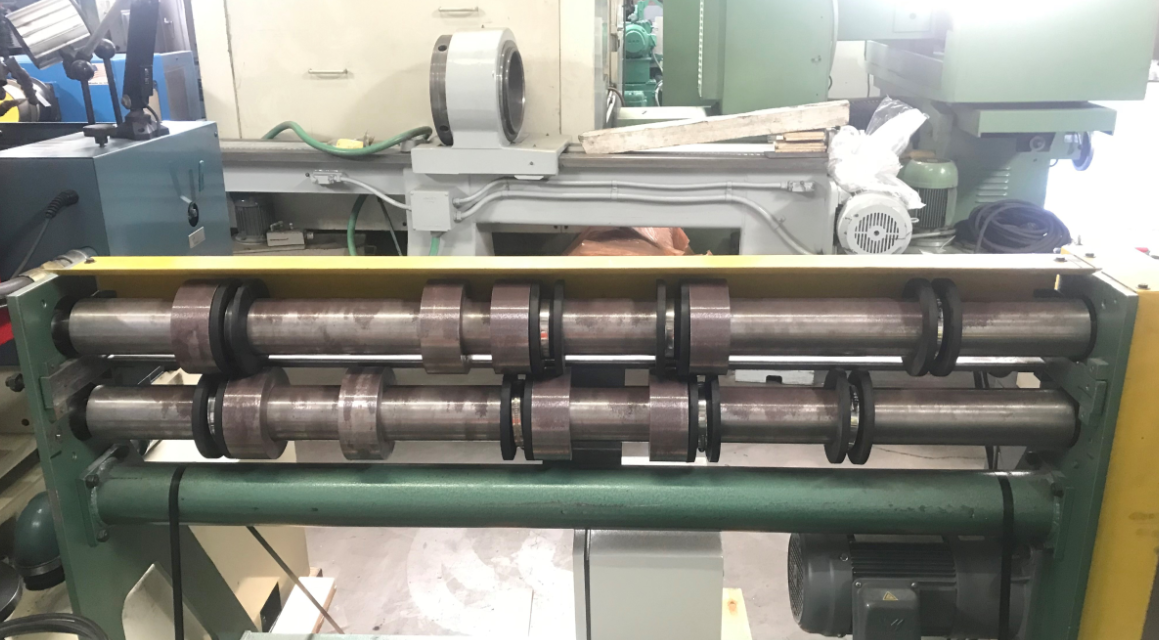
Operating a gang slitter is an intricate task that requires a keen understanding of both the machinery and the safety protocols that protect the operators and the surrounding workforce. At Hengli, we prioritize safety and efficiency, ensuring that our operators are well-equipped with the knowledge and skills necessary for optimal performance. This article delves into the best practices for operating a gang slitter, emphasizing the importance of safety first.
Understanding the Gang Slitter
A gang slitter is a specialized and powerful machine widely utilized in industries such as manufacturing, metal processing, and paper production. Its primary function is to cut large rolls of material, often referred to as master coils, into narrower strips or widths that are more manageable and suitable for subsequent processing or end-use applications. This process is essential in various production lines where precise material sizing is critical.
The effectiveness and efficiency of a gang slitter depend significantly on both its design and the functionality of its components.Additionally, the tension control systems, winding mechanisms, and material handling features play a crucial role in achieving consistent and high-quality output.
A skilled operator must have a thorough understanding of the machine's capabilities, limitations, and safety protocols. Proper setup, maintenance, and operation of the gang slitter are vital not only for optimizing productivity but also for preventing accidents and ensuring a safe working environment. This includes regular inspections, adherence to safety standards, and continuous monitoring of the machine's performance during operation.
Key Components of a Gang Slitter
- Blades: The heart of the slitting process. High-quality blades ensure clean cuts and reduce the risk of jams or accidents.
- Rollers: These guide the material through the machine and play a vital role in maintaining tension.
- Drive Mechanism: Responsible for the movement of the blades and rollers, ensuring precise operation.
- Control Panel: Provides operators with the necessary controls to adjust settings and monitor performance.
- Safety Guards: Essential for protecting operators from moving parts and potential hazards.
Pre-Operational Safety Checks
Before engaging the gang slitter, it is crucial to conduct thorough pre-operational safety checks. This proactive approach minimizes risks and ensures that the equipment is functioning correctly.
1. Inspect the Equipment
Before operating a gang slitter, it is crucial to thoroughly inspect the equipment to ensure safe and efficient performance. Begin by checking the blades for any signs of wear or damage, as dull or compromised blades can increase the risk of accidents. Next, inspect the rollers to ensure they are clean and functioning smoothly, free of debris that could impede operation. The control panel should also be verified to confirm that all buttons and emergency stops are fully operational. Lastly, ensure that all safety guards are properly in place and undamaged, as these are vital for protecting the operator from potential hazards.
2. Review Safety Protocols
Implementing Lockout/Tagout (LOTO) procedures is essential for maintaining safety during the maintenance of a gang slitter, ensuring that the machine is completely de-energized and cannot be accidentally activated while repairs or inspections are being conducted. This procedure protects workers from hazardous energy releases that could cause injury.
Additionally, it is vital to be well-versed in emergency procedures, which involve knowing how to quickly and effectively respond in the event of an accident or equipment failure. This includes understanding the location and use of emergency stops, first aid protocols, and the steps to safely shut down the machine to prevent further harm.
3. Personal Protective Equipment (PPE)
Wearing the appropriate PPE is non-negotiable. Operators should do:
- Safety Glasses: Protect eyes from flying debris.
- Gloves: Ensure a firm grip while handling materials.
- Steel-Toed Boots: Protect feet from heavy materials and equipment.
- Hearing Protection: Reduce the risk of hearing loss in noisy environments.
Operational Best Practices
Once the pre-operational checks are complete, operators can proceed with the gang-slitting process. Adhering to best practices during operation is essential for maintaining safety and efficiency.
1. Proper Material Handling
Loading Materials: Ensure that materials are loaded evenly to prevent jams. Use mechanical assistance when handling heavy rolls.
Tension Control: Maintain proper tension on the material to avoid slippage or uneven cuts.
2. Monitor Machine Performance
Regular Checks: Continuously monitor the machine for unusual noises or vibrations that may indicate a malfunction.
Adjustments: Make necessary adjustments to blade height and tension based on the material being processed.
3. Communication
Effective communication among team members is vital. Operators should:
Use Hand Signals: Establish clear signals for operating the machine, especially in noisy environments.
Conduct Regular Briefings: Hold meetings to discuss safety protocols and any updates on operational procedures.
4. Emergency Preparedness
Operators must be prepared for emergencies. This involves:
Location of Emergency Stops: Familiarize yourself with the location of emergency stop buttons and how to use them.
First Aid Kits: Ensure that first aid kits are easily accessible and stocked with necessary supplies.
Post-Operational Procedures
Maintaining a clean and organized work area is crucial for safety and efficiency when operating a gang slitter. Start by removing any debris or scraps from the area to prevent slips, falls, or other accidents. Additionally, it's important to inspect the equipment and surrounding area for any signs of wear or damage that may have occurred during operation, addressing any issues promptly to avoid further complications.
Regular maintenance checks include sharpening or replacing blades to ensure cutting efficiency and lubricating all moving parts to prevent excessive wear and tear. Documenting operations is key to identifying trends or potential issues. Keeping accurate records of the types of materials processed and tracking operational hours can help in scheduling timely maintenance and improving overall machine performance.
Conclusion
Operating a gang slitter safely and efficiently is a multifaceted endeavor that requires a commitment to best practices and continuous improvement. By prioritizing safety, conducting thorough pre-operational checks, and fostering a culture of communication and training, organizations can enhance the safety and productivity of their operations.
At Hengli, we are dedicated to providing the resources and training necessary to ensure that our operators can perform their tasks with confidence and skill. By adhering to these best practices, we can collectively ensure a safe working environment and optimal operational efficiency.
The above briefly introduces the safety precautions of the slitting machine. If you want to know more or purchase slitting machine equipment, please contact us.
Hengli is a leading gang-slitting machine manufacturer. Hengli takes innovation as the guide and cutting-edge technology as the guide. Its main product series is seamlessly connected with the world's advanced technology and is widely used in key areas of the national economy such as automobile manufacturing and parts processing, steel metallurgy processing, electricity, and metal packaging. With the vision of becoming a pioneer in the metal felt forming industry, Hengli is unswervingly committed to innovation and brand building to promote the prosperity and development of China's equipment manufacturing industry.
Hengli puts innovation first, unswervingly focuses on technological progress, strives to become a technological pioneer and market leader, promotes the progress of China's equipment manufacturing industry, and sets new standards for quality and performance in the global market.