How to Solve Common Sheeting Line Problems
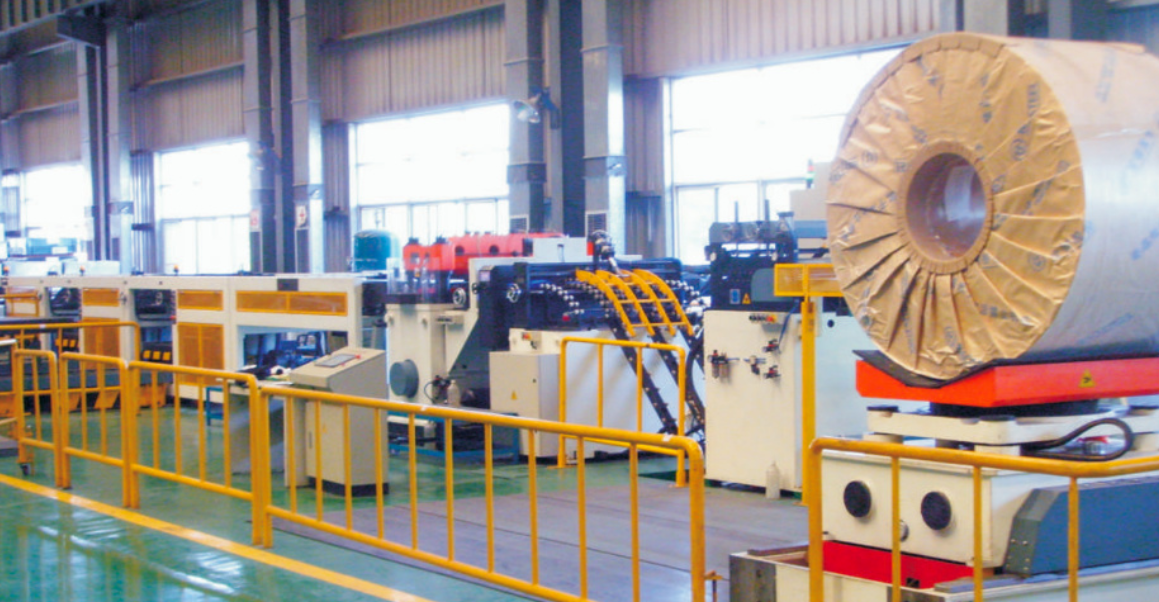
In the manufacturing industry, sheeting lines play a vital role in the production of a variety of materials, including paper, plastics, and metals. However, these lines often encounter a range of common problems that can affect efficiency and affect product quality. At Hengli, we understand the importance of promptly addressing these issues to maintain productivity and profitability. In this comprehensive guide, we will explore the most common problems faced by sheeting lines and provide effective solutions for each.
1. Calendering Line Misalignment
Misalignment can be caused by improper installation or worn components. Common causes include inaccurate setup, improper positioning during installation leading to misalignment, and worn components such as rollers and guides, which can age over time and cause misalignment issues.
Solutions to Misalignment Problems
To correct misalignment problems, regular maintenance should be performed to check and ensure that all components are properly aligned. In addition, using adjustable guides and rollers can allow for fine-tuning during operation, while following the manufacturer's guidelines and using accurate measuring tools during installation can help prevent misalignment from the beginning.
2. Inconsistent Sheet Thickness
Inconsistent sheet thickness can lead to product defects and customer dissatisfaction, which is usually caused by inconsistent material quality (differences in raw materials affect thickness) and improper calibration of sheet production lines (causing thickness changes during the manufacturing process).
Technology to Ensure Consistent Thickness
In order to maintain uniform sheet thickness, it is necessary to implement technologies such as raw material quality control, by purchasing high-quality materials and checking them regularly, investing in automatic calibration systems, continuously monitoring and adjusting thickness during production, and training operators to ensure that they can quickly identify and resolve thickness issues.
3. Paper Wrinkling and Curling
Wrinkling and curling can seriously affect the appearance and functional quality of paper. This is usually caused by incorrect tension settings. Too much or too little tension can cause deformation, and environmental factors (such as changes in humidity and temperature) can also cause paper curling.
Measures to Prevent Wrinkling and Curling
In order to prevent paper wrinkling and curling, it is important to implement advanced tension control systems to maintain optimal tension throughout the process, regulate the humidity and temperature of the production area to minimize environmental impact and select materials that are not prone to curling and wrinkling.
4. Equipment Downtime
Downtime is a major challenge for sheet metal production lines, resulting in lost production time and increased costs. Common causes include mechanical failure (unexpected failures disrupt operations) and maintenance issues (inadequate scheduled maintenance can cause equipment failure).
Strategies to Reduce Downtime
To reduce equipment downtime, it is important to establish a preventive maintenance program that addresses potential issues before they lead to failures, leverage IoT sensors to monitor equipment health and performance in real-time, and train employees to perform minor troubleshooting and maintenance tasks.
5. Poor laminate Adhesion
Poor laminate adhesion can severely compromise the integrity of the product and is often caused by factors such as surface contamination, where dirt or oil on the surface prevents proper bonding, and improper adhesive application, resulting in weak adhesion and insufficient performance.
Improving Bond Quality
To improve the quality of laminate bonds, it is important to ensure that surfaces are thoroughly cleaned and prepared before applying adhesive, use high-quality adhesives appropriate for the materials being laminated, and provide operators with training on proper adhesive application techniques.
6. Low Production Speed
Slow production speeds can seriously hinder overall output and profitability. Common reasons include slow machine speeds, suboptimal levels, which reduce efficiency, and bottlenecks in the process. Identifying and resolving these limitations is critical to ensuring smooth operations.
Increasing Production Speeds
To increase production speeds, it is important to invest in modern machinery designed to increase speed and efficiency, analyze workflows to optimize processes and eliminate bottlenecks, and train employees on best practices for efficient machine operation.
Conclusion
Solving common problems in sheet metal production lines is critical to maintaining efficiency and product quality. At Hengli, we are committed to providing comprehensive solutions to meet the unique challenges facing the industry. By implementing the strategies outlined in this guide, manufacturers can significantly improve sheet metal production line operations, reduce downtime, and improve product quality. Adopt these best practices and take your production capabilities to new heights.
Hengli is a professional sheet metal shearing equipment manufacturer that focuses on continuous improvement and innovation, ready to meet your sheet metal production line needs and help you cope with the complexity of modern manufacturing. We want to provide the right solution that fits the actual situation of your business. We will listen carefully to your requirements and work with you to identify all aspects that need to be addressed, including material, operation, operator, and packaging considerations. We focus on providing reliable machines to increase your productivity, reduce waste and improve output quality. If you are looking for reliable sheet metal shearing equipment, welcome to contact us.