Decoding the Challenges and Solutions in Automotive Inner and Outer Panel Blanking
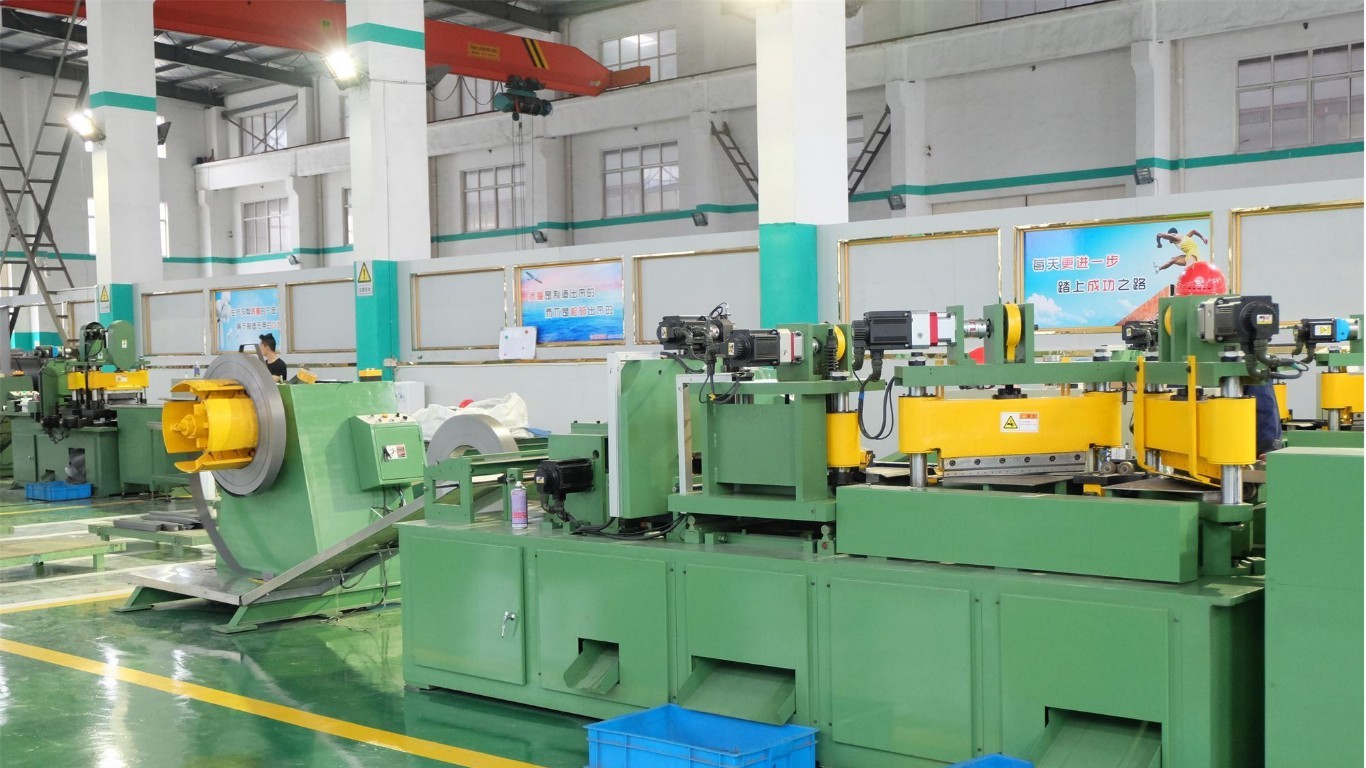
Automotive inner and outer panels are crucial components of the car body structure, and the quality of their stamping directly impacts the vehicle's safety and aesthetics. Blanking, the first step in the stamping process, plays a vital role. However, with the increasing demand for lightweight and personalized vehicles, automotive inner and outer panel blanking faces growing challenges. This article delves into these challenges and presents corresponding solutions leveraging HENGLI's advanced technologies and products.
Challenges in Automotive Inner and Outer Panel Blanking:
High Precision and Complex Shapes: Modern car designs are becoming increasingly intricate, resulting in more diverse inner and outer panel shapes. Curves, arcs, and irregularly shaped holes add to the complexity, demanding higher blanking precision. Traditional blanking processes struggle to meet the requirements for these high-precision, complex parts.
Lightweight Materials: To improve fuel efficiency and reduce emissions, lightweight materials such as high-strength steel and aluminum alloys are increasingly used in automotive manufacturing. These materials possess different machining characteristics compared to traditional steel, presenting new challenges for blanking equipment and tooling. For instance, the high hardness of high-strength steel can cause significant tool wear, while aluminum alloys are prone to sticking to the tooling.
Production Efficiency and Cost Control: In a competitive market, automakers must continuously improve production efficiency and reduce manufacturing costs. As a key process in the stamping line, blanking efficiency directly affects the overall production capacity. Furthermore, material utilization is a critical factor influencing cost.
Automation and Intelligence: With the rise of Industry 4.0 and smart manufacturing, the automotive industry is moving towards automation and intelligence. The level of automation in the blanking process directly impacts the flexibility and efficiency of the production line.
HENGLI's Solutions:
As a leading supplier of metal sheet cutting and forming automation equipment, HENGLI focuses on the research and development of high-end industrial automation equipment. With extensive experience in metal sheet cutting and forming automation, HENGLI offers the following solutions to address the challenges in automotive inner and outer panel blanking:
High-Precision CNC Blanking Equipment: HENGLI's blanking equipment utilizes advanced CNC systems and high-precision servo motors, enabling high-precision, high-speed blanking to meet the demands of complex part geometries. For example, HENGLI's "Automotive Inner and Outer Panel Blanking Unit" can be customized to customer requirements and integrated into automated production lines.
Material-Specific Tooling and Processes: HENGLI provides professional tooling selection and process optimization solutions tailored to different materials. For high-strength steel, wear-resistant cemented carbide tools are employed. For aluminum alloys, specialized coated tools are used to prevent sticking and cutting parameters are optimized to ensure processing quality.
Automated Blanking Lines: HENGLI offers fully automated blanking line solutions that integrate decoiling, leveling, feeding, blanking, and stacking functions. This enables unmanned operation, significantly improving production efficiency and reducing labor costs. The "Press Blanking Line/Automatic Blanking (Swing) Line/Blanking Line" product series is designed specifically for this purpose.
Modular Swing Beam Shears: HENGLI's modular swing beam shears offer flexible configuration and high cutting efficiency. They can be customized to meet the cutting needs of different sheet sizes and shapes, improving material utilization.
Precision Tools and Inspection Instruments: HENGLI provides high-precision slitting dies/tools and inspection instruments, such as the "Pinhole Detector," which can accurately inspect sheet metal, ensuring product quality and providing data support for process optimization.
HENGLI's Product Advantages:
Advanced Technology from Japan: HENGLI, through its wholly-owned subsidiary, SUMIKURA, inherits 70 years of experience and technological expertise in the automotive manufacturing industry, guaranteeing product quality.
Customized Solutions: HENGLI offers customized blanking solutions based on specific customer needs, including equipment selection, process flow design, and automation integration, helping customers achieve optimal production efficiency.
Comprehensive After-Sales Service System: HENGLI provides comprehensive after-sales service, including equipment installation and commissioning, operator training, maintenance, and spare parts supply, ensuring stable operation of customer equipment.
Conclusion:
The continuous development of automotive inner and outer panel blanking technology places higher demands on equipment and processes. With advanced technology, extensive experience, and comprehensive service, HENGLI is committed to providing efficient, precise, and reliable blanking solutions, contributing to the advancement and development of the automotive manufacturing industry. Contact us to learn more.
Material: Silicon-steel, tinplate, strip steel and aluminum strip, etc
Slitting thickness: 0.2-1.5mm
Slitting width: ≥30mm