The Challenges and Solutions of Automotive Panel Blanking Processes
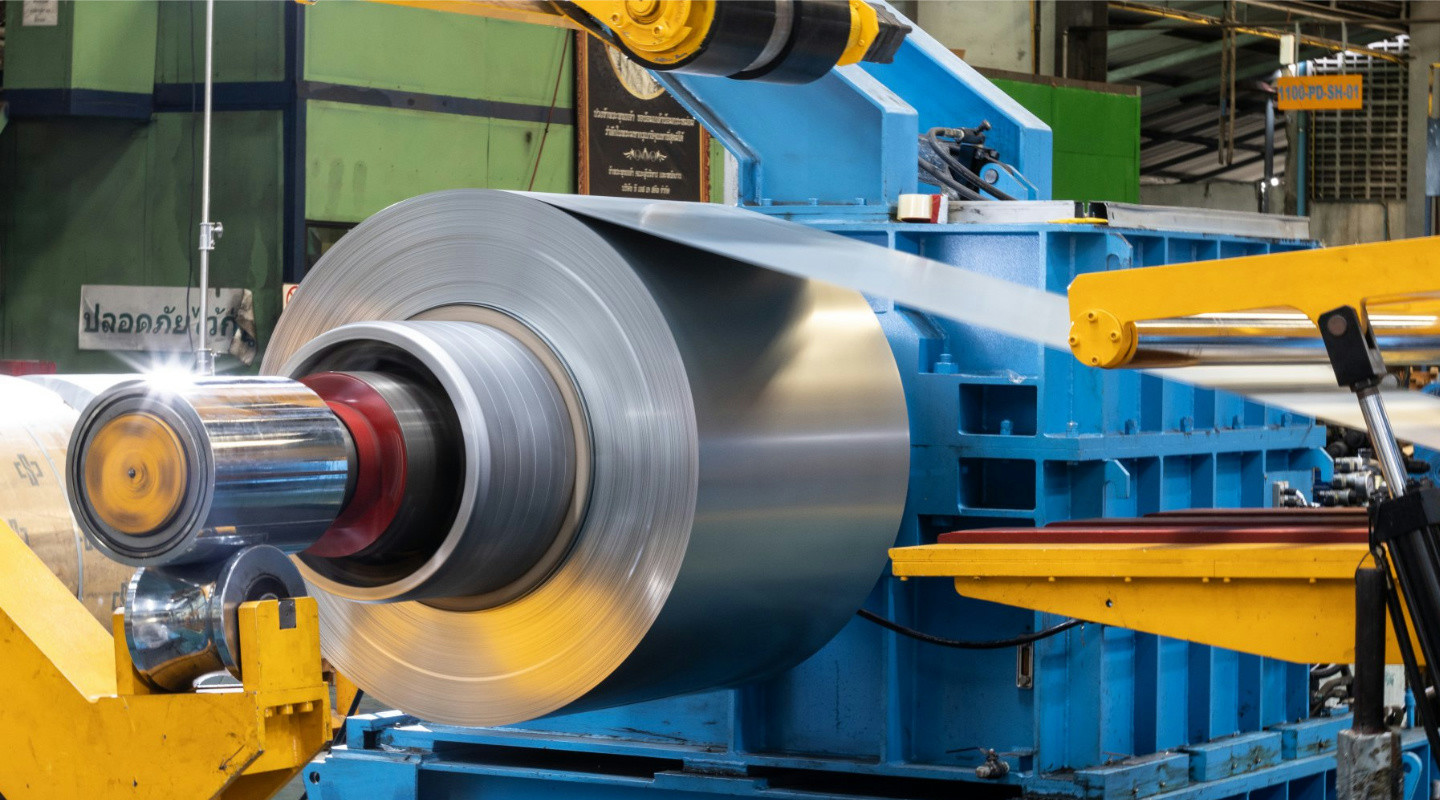
The automotive industry is becoming increasingly competitive, with consumers demanding higher quality, enhanced performance, and innovative designs. Precision and efficiency in blanking processes for interior and exterior panels play a vital role in determining the overall quality, performance, and cost-effectiveness of a vehicle. This article highlights the challenges in automotive panel blanking processes and examines how HENGLI with over 70 years of industry expertise, provides customized solutions to address these challenges effectively.
Challenges in Automotive Panel Blanking Processes
1. Balancing High Precision and Complex Shapes
Modern vehicles emphasize streamlined designs, intricate curves, and advanced aesthetics, requiring exceptional precision in the blanking process. Utilizing automotive panel blanking machines that ensure high accuracy for complex shapes is crucial to avoiding defects and meeting consumer expectations. According to the J.D. Power 2023 Initial Quality Study, exterior defects remain a leading concern for car buyers, underscoring the importance of precision in blanking processes.
2. Adapting to Diverse Material Properties
Automotive panels are fabricated using materials like high-strength steel, aluminum alloys, and composites, each presenting unique challenges in forming and cutting. HENGLI's advanced sheet shearing machines and material-specific optimization techniques ensure seamless adaptation to these material properties, preventing issues such as cracking and wrinkling.
3. Efficiency and Cost Control
To stay competitive, manufacturers must boost efficiency while managing costs. This involves reducing waste, minimizing energy consumption, and leveraging advanced technology, such as automatic shear line machines, to optimize production rates. The integration of efficient systems can significantly enhance productivity without compromising on quality or increasing operational costs.
4. Automation and Smart Upgrades
Industry 4.0 demands smart manufacturing solutions. HENGLI incorporates cutting-edge automation, utilizing rotary shear lines and intelligent control systems that streamline the blanking process. According to McKinsey, as much as 80% of manufacturing processes could be automated by 2030, highlighting the critical role of intelligent solutions in driving efficiency and reducing manual intervention.
5. Equipment Stability and Maintenance
Stable operation of hydraulic shearing machines and other blanking equipment is vital for uninterrupted production. Downtime caused by equipment failure leads to costly delays. Regular maintenance and advanced diagnostic systems ensure equipment reliability and reduce operational disruptions.
HENGLI's Customized Solutions
With expertise in metal sheet cutting and forming automation, HENGLI offers a comprehensive range of tailored solutions designed to meet the diverse needs of automotive manufacturers:
1. High-Precision Uncoiling and Blanking Lines
HENGLI's automotive panel blanking machines combine high-precision servo motors and advanced hydraulic shearing technology. These systems achieve a blanking accuracy of ±0.1mm, minimizing material waste and reducing production costs.
2. Flexible Rotary Shear Lines
HENGLI's rotary shear line features a quick die-change system, allowing mold changes in under 15 minutes. This system efficiently handles various shapes, including rectangular, trapezoidal, and curved panels, enhancing flexibility for manufacturers producing multiple designs.
3. Intelligent Blanking Control Systems
Leveraging Industrial IoT, HENGLI's intelligent systems collect real-time production data to optimize parameters for automatic shear line machines. By utilizing AI-driven algorithms, manufacturers can improve production efficiency and material utilization, achieving significant gains in output quality.
4. Advanced Die Design and Manufacturing
HENGLI's team uses CAD/CAM/CAE technology to design and produce long-lasting dies for sheet shearing machines. These durable dies, crafted from carbide materials, withstand up to 1 million stamping cycles, ensuring consistent performance and reducing downtime.
5. Full Lifecycle Service and Support
HENGLI offers end-to-end support, from installation and commissioning to preventive maintenance and operator training. Remote diagnostics and quick spare part availability ensure uninterrupted operation of hydraulic shearing machines and other equipment.
Why Choose HENGLI?
By choosing HENGLI, you're partnering with an industry leader offering reliable, innovative, and customized solutions for blanking and shearing processes. With cutting-edge technologies and a focus on client success, HENGLI empowers manufacturers to overcome operational challenges, achieve production excellence, and maintain a competitive edge.
Contact HENGLI today to learn more about our automotive shearing machines, rotary shear lines, and tailored blanking solutions designed for your manufacturing needs.
Shearing line: 150 sheets/min, 3 stackers, with pinhole detector, motorized digital inspection table, quick die change system