Crafting the Perfect Shearing Line – Hengli's Tailored Approach
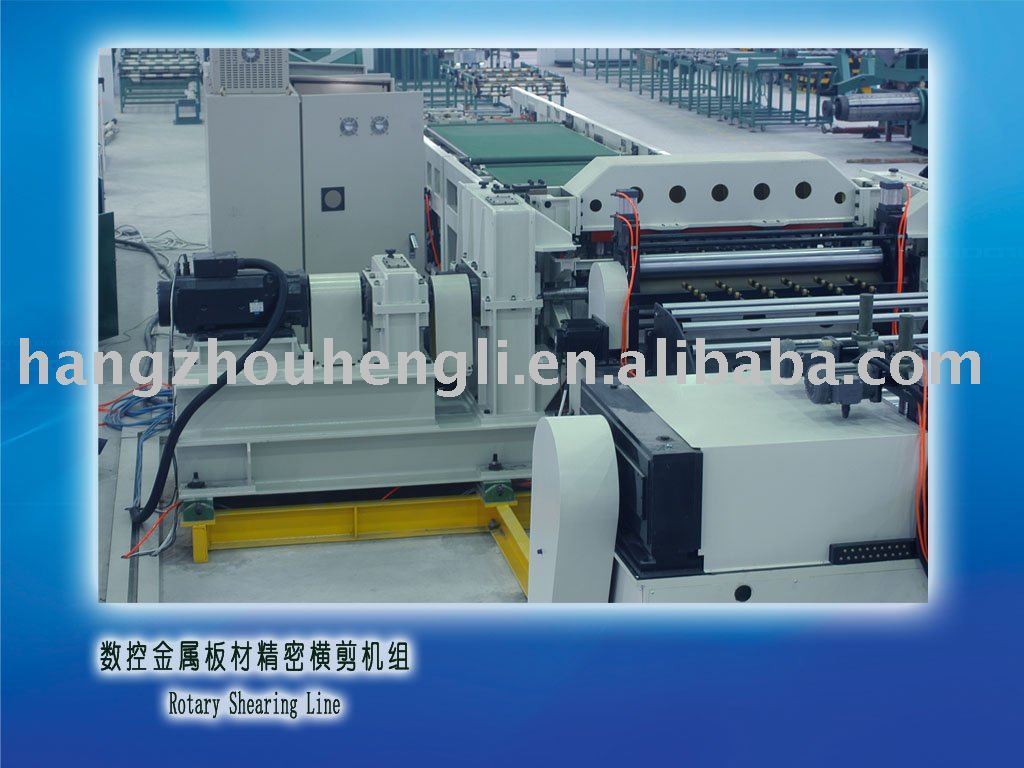
In the world of metal processing, precision and efficiency are paramount. Off-the-shelf solutions can often fall short, leaving you with compromises in performance, material utilization, and overall productivity. At Hengli, we understand that your needs are unique. That's why we go beyond simply offering a catalog of equipment; we specialize in crafting customized shearing production lines designed to seamlessly integrate into your specific operations.
So, how does Hengli approach the customization process? It's a collaborative journey that begins with a deep understanding of your challenges and aspirations.
Step 1: The Discovery Phase – Understanding Your "Why"
Before we even begin discussing equipment specifications, we focus on understanding your "why." What are your specific goals? What materials are you working with? What are the key challenges you face in your current shearing processes?
Our team of experienced engineers will engage in detailed consultations with your team to gather critical information, including:
Material Specifications: Type of metal (e.g., cold-rolled steel, hot-rolled steel, stainless steel, silicon steel, tinplate, aluminum), thickness range, and surface finish requirements.
Blanking Requirements: Desired blank shapes and sizes, tolerance requirements, and edge quality specifications.
Production Volume: Required throughput, cycle times, and overall production capacity.
Automation Level: Desired level of automation, from manual operation to fully automated systems with robotic handling.
Space Constraints: Available floor space and layout considerations.
Budgetary Considerations: Project budget and ROI expectations.
Step 2: Solution Design – Engineering the Optimal System
Once we have a thorough understanding of your needs, our engineers will leverage their expertise and cutting-edge design tools to develop a customized shearing line solution. This may involve:
Selecting the Right Equipment: Choosing the appropriate shearing machine (e.g., rotary shear, flying shear, oscillating shear, modular swing beam shear) based on your material and blanking requirements.
Integrating Automation: Incorporating automation components such as coil handling systems, automatic feeding mechanisms, robotic stacking systems, and online inspection systems to maximize efficiency and minimize manual labor.
Custom Tooling Design: Design specialized tooling (e.g., scroll/straight dies, slitting dies) to achieve the desired blank shapes and edge quality.
Optimizing Line Layout: Designing the optimal line layout to minimize material handling, reduce cycle times, and maximize space utilization.
Incorporating Quality Control: Integrating pinhole detectors, surface inspection systems, and other quality control measures to ensure consistent output quality.
Step 3: Manufacturing and Testing – Precision and Reliability
Our state-of-the-art manufacturing facility is equipped with advanced CNC machining centers, welding robots, and other precision equipment. We adhere to strict quality control standards throughout the manufacturing process to ensure that every component meets our exact specifications.
Before shipment, each shearing line undergoes rigorous testing to verify its performance and reliability. This includes:
Functional Testing: Verifying that all equipment components are functioning correctly.
Performance Testing: Measuring throughput, cycle times, and other performance metrics.
Accuracy Testing: Verifying the accuracy of blank shapes and sizes.
Safety Testing: Ensuring that the system meets all relevant safety standards.
Step 4: Installation and Training – Seamless Integration
Our team of experienced technicians will handle the installation and commissioning of your customized shearing line at your facility. We will also provide comprehensive training to your operators and maintenance personnel to ensure that they are fully capable of operating and maintaining the system.
Step 5: Ongoing Support – Your Partner for Success
At Hengli, we are committed to providing ongoing support to our customers. We offer:
Spare Parts: A comprehensive inventory of spare parts to minimize downtime.
Technical Support: 24/7 technical support via phone, email, or remote access.
Preventive Maintenance: Scheduled maintenance services to ensure the long-term reliability of your equipment.
Upgrades and Retrofits: Opportunities to upgrade or retrofit your existing shearing line to improve its performance or extend its lifespan.
The Hengli Advantage: Tailored Solutions, Tangible Results
As a professional manufacturer, HengLi provides high-performance shearing lines and customized solutions based on customer needs. By choosing Hengli Technology, you're not just buying a piece of equipment; you're investing in a customized solution that will deliver tangible results, including:
Increased Productivity: Higher throughput and shorter cycle times.
Improved Material Utilization: Reduced cut waste and optimized blank nesting.
Enhanced Quality: Consistent blank shapes, sizes, and edge quality.
Reduced Labor Costs: Automation reduces the need for manual labor.
Improved Safety: Automated systems minimize the risk of operator injury.
Ready to take your shearing operations to the next level? Contact Hengli Technology today to discuss your specific needs and explore the possibilities of a customized shearing line solution.
Shearing line: 150 sheets/min, 3 stackers, with pinhole detector, motorized digital inspection table, quick die change system
1. Material: tinplate/aluminium
2.material thickness:0.125~0.525mm
3.sheet width:500~1200mm
4.line speed: 56SPM