Selection and Maintenance of Slitting Dies: Enhance Cutting Quality and Efficiency
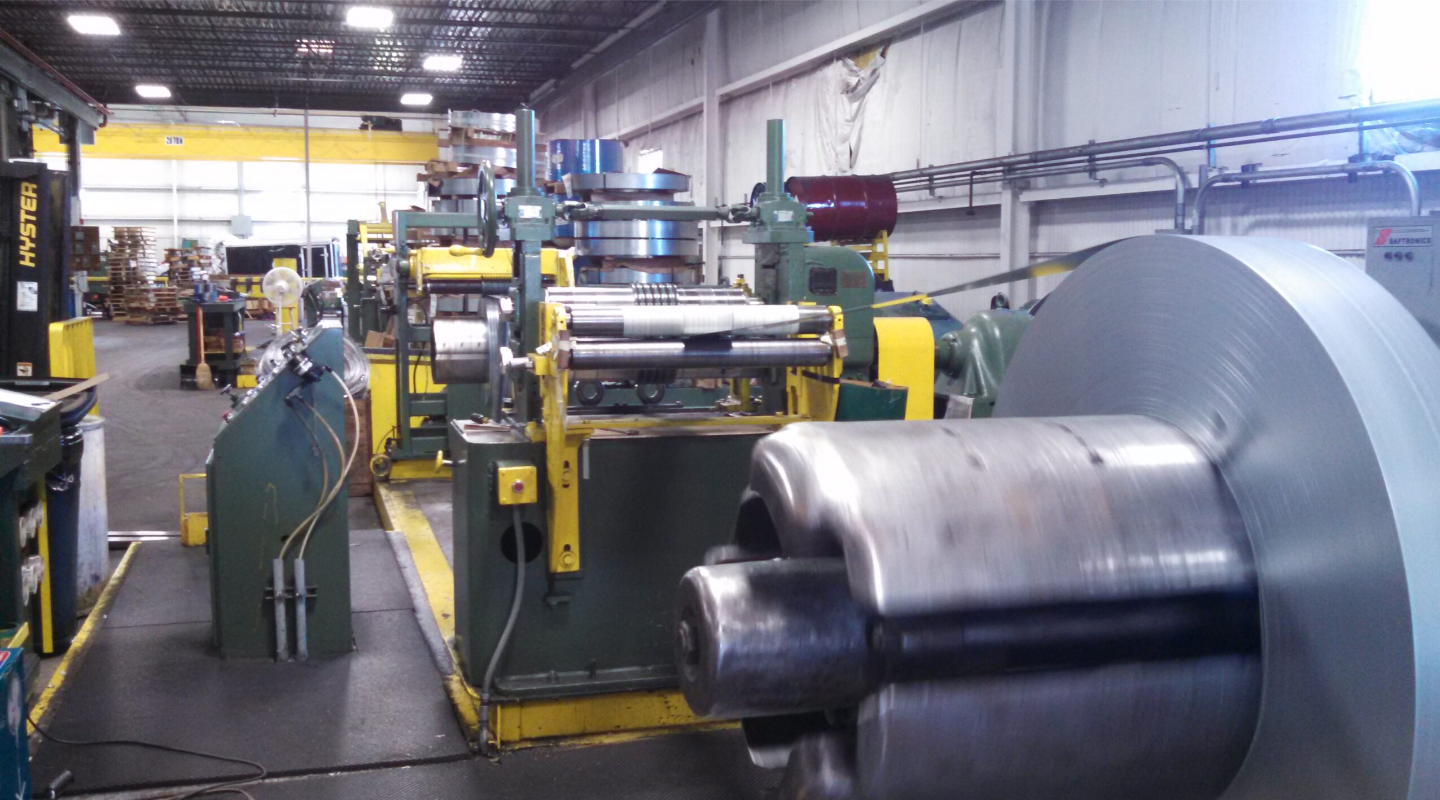
The slitting process is essential in metal sheet processing, and the choice and maintenance of slitting dies directly impact cutting precision, production efficiency, and equipment lifespan. Selecting the right die and maintaining it properly is crucial for optimizing manufacturing operations. This guide explores key factors in slitting die selection and maintenance, offering comprehensive solutions for metal processing businesses.
Types and Characteristics of Slitting Dies
1. Rotary Disc Blades
Features: Simple structure, easy to replace, and widely applicable.
Suitable Materials: Cold-rolled steel, hot-rolled steel, stainless steel, aluminum.
Limitations: Lower cutting accuracy, prone to burrs.
2. Straight-Edged Blades
Features: High cutting accuracy, clean cut edges, suitable for precision applications.
Suitable Materials: Silicon steel, copper.
Limitations: Complex structure, difficult to replace, higher cost.
3. Combination Dies
Features: Flexible tool configurations for various cutting needs.
Suitable Materials: Multiple metal types.
Limitations: Complex design, higher maintenance requirements.
Key Factors in Choosing the Right Slitting Die
1. Material Characteristics
Hardness: Choose suitable blade materials like high-speed steel or carbide based on metal hardness.
Thickness: Match blade size and clearance to material thickness.
Surface Quality: Select appropriate edge profiles for different surface finishes.
2. Cutting Precision
Dimensional Accuracy: Use high-precision blades and guiding mechanisms.
Edge Quality: Opt for sharp-edged blades and optimized cutting parameters.
Burr Control: Adjust blade clearance and lubrication for minimal burrs.
3. Production Efficiency
Cutting Speed: High-speed blades and automated lines improve throughput.
Tool Change Time: Modular designs enable faster blade replacement.
Automation: Automated slitting lines enhance precision and consistency.
4. Cost Management
Tool Longevity: Durable materials extend blade life.
Maintenance Costs: Choose dies with easy maintenance.
Procurement Budget: Balance performance and cost-effectiveness.
Maintenance and Care of Slitting Dies
1. Daily Maintenance
Cleaning: Remove debris and oil residues after use.
Lubrication: Apply lubricant regularly to reduce friction.
Inspection: Check blade sharpness and clearance periodically.
2. Regular Servicing
Grinding: Sharpen blades periodically to maintain cutting quality.
Replacement: Change damaged or severely worn blades in time.
Adjustment: Align blade clearance and guiding devices for precision cuts.
3. Best Practices
Proper Usage: Follow operational guidelines to prevent overloading.
Safety Measures: Implement protective measures to avoid injuries.
Professional Maintenance: Schedule expert servicing for optimal performance.
Hengli's Slitting Solutions: Optimizing Performance
As a leader in metal sheet cutting and automation, Hengli provides high-precision slitting dies and production lines designed for efficiency and durability.
High-Precision Blades: Manufactured with premium materials and advanced processes for an extended lifespan.
Modular Design: Simplifies blade replacement and maintenance.
Automated Control: Advanced automation improves cutting speed and accuracy.
Custom Solutions: Tailored die and slitting line configurations to meet specific production requirements.
Conclusion
Selecting and maintaining the right slitting die is essential for improving cutting quality and operational efficiency. Hengli delivers top-tier slitting solutions to optimize production lines and enhance competitiveness. Contact Hengli today for expert consultation and customized slitting solutions.
Scroll Die: Integral carbide, can be used in Hengli line, Littell line, Japanese flying cutting line